Options
Mallikarjuna J M
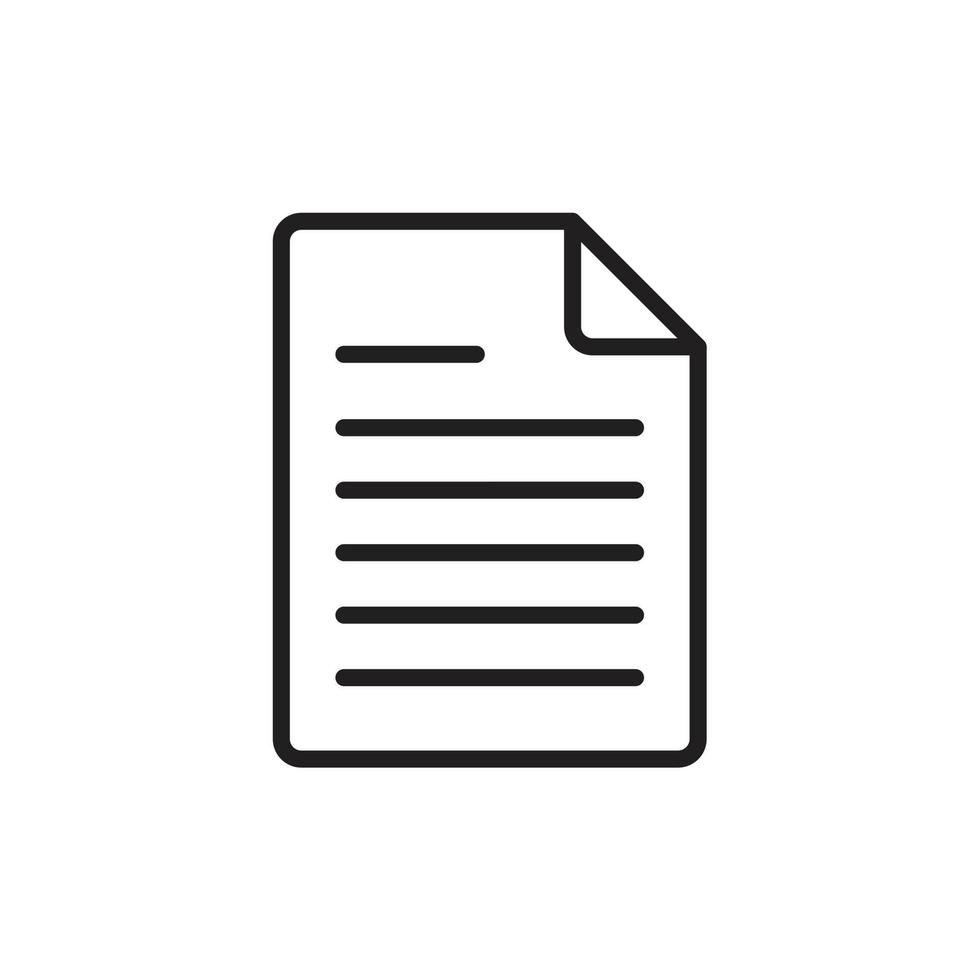
Effect of piston shape on scavenging in a two-stroke engine - A CFD analysis
01-01-2014, Agrawal, Vivek, Mallikarjuna J M
This study focuses on effect of piston shape on in-cylinder flows in a conventional loop scavenged two-stroke engine using CFD. Three piston-shapes viz., flat, flat with center-bowl and flat with center-dome are analyzed along with a standard piston. The CFD solution has been obtained by using commercial CFD code STAR-CD. First, the CFD results are compared with those of experimental values obtained from particle image velocimetry (PIV). For comparison among various piston shapes, various parameters viz., velocity vector plots, tumble ratio (TR), turbulent kinetic energy (TKE) at various crank angles are used. Scavenging and trapping efficiencies are also calculated for each piston configuration. From the results, it is found that flat with center-bowl piston is the best in terms of in-cylinder flow characteristics. It gives higher TR and TKE with very little effect on efficiencies. © (2014) Trans Tech Publications, Switzerland.
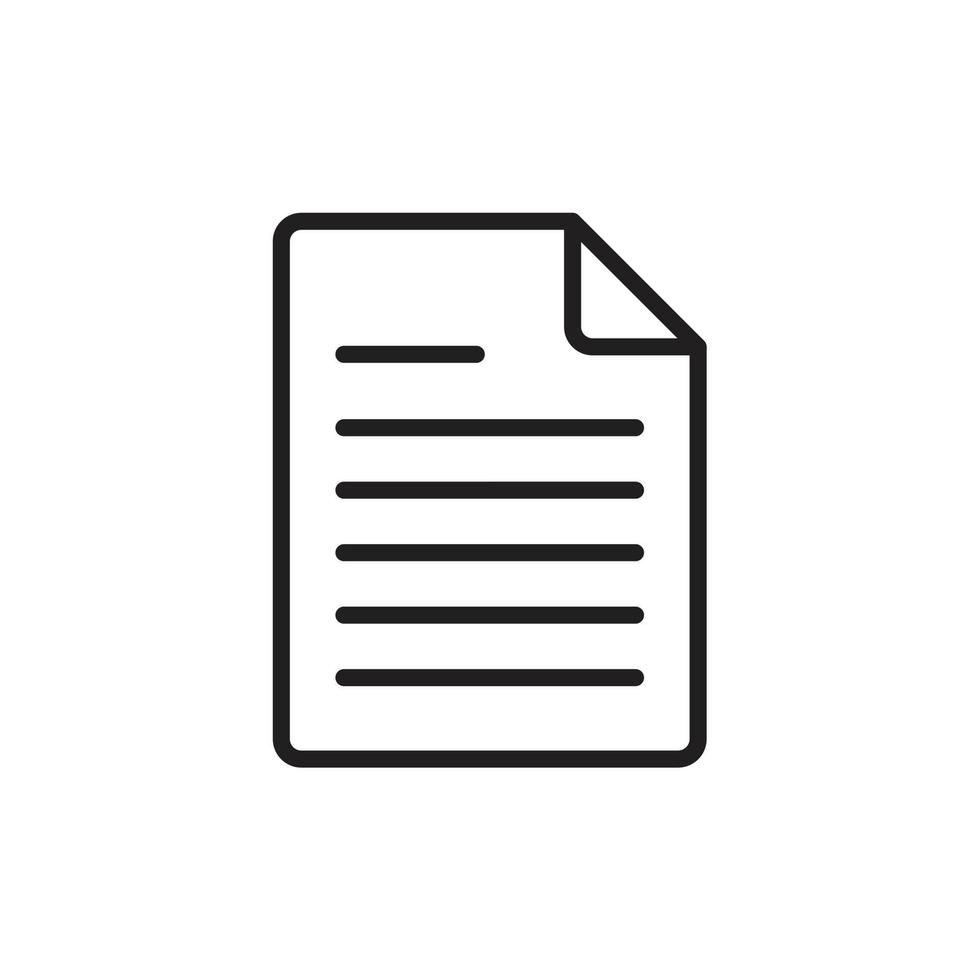
Effect of housing size on the performance of a centrifugal compressor for turbocharger application: An experimental and numerical study
01-08-2022, Karunakaran, Ealumalai, Mallikarjuna J M
Currently, engine downsizing through turbocharging is widespread in the automotive industry to improve fuel economy and emissions. The engine downsizing demands compact and high performance centrifugal compressors for turbochargers. A compressor contains mainly an impeller and housing, which often uses a vaneless diffuser and an overhanging volute. High-speed flow from the impeller is decelerated in the diffuser and volute, to recover static pressure for boosting the engine. The volute flow characteristics and pressure recovery depend on the housing size, which determines the overall compressor performance and size. This study evaluates the effect of four different housing sizes viz., baseline, 12% scaled up, and 12% and 20% scaled-down geometrically, through experimental and numerical analysis. The experiments are conducted using different housing sizes with a given impeller to measure the compressor pressure ratio and efficiency. Also, steady-state numerical simulations are performed to examine the flow mechanisms causing pressure losses due to changes in housing size. Then, the simulation is also done for different volute surface roughness levels in each housing to establish its effect on compressor performance. From the results, it is found that there is no marked change in compressor efficiency between the baseline and 12% scaled-up housing. Whereas, the scaled-down housings (12% and 20%) showed efficiency drop of about 2–5 percentage points at near-choke flow rate. The CFD analyses of these scaled down housings with reduced cross-sectional area indicated substantial increase of meridional velocity, which results in higher swirl velocity in the volute causing more pressure losses. Besides, the increased volute surface roughness is realized to cause extra pressure loss due to higher wall shear stress. It amounts to additional efficiency reduction of 0.5–1 percentage points at the same near-choke flow.
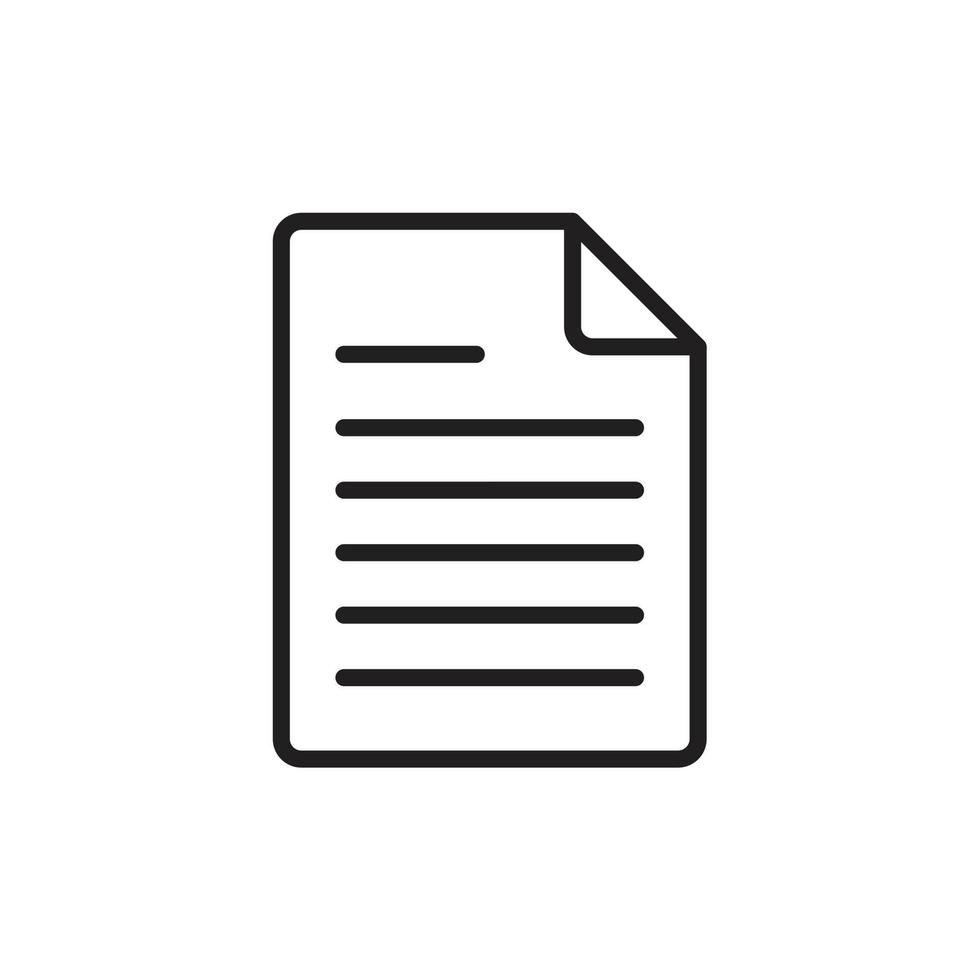
Effect of in-cylinder air-water interaction on water evaporation and performance characteristics of a direct water injected GDI engine
01-04-2021, Raut, Ankit A., Mallikarjuna J M
Water injection is one of the promising strategies for modern downsized GDI engines to meet performance and emission requirements under wide operating conditions. However, the benefits of water injection strongly depend upon water evaporation and distribution of water vapours inside the combustion chamber. In this regard, water injector location and orientation are two significant geometrical parameters which decide the in-cylinder positioning of the water spray, evaporation, and vapour distribution. Therefore, this CFD study presents the effects of water injector location, and orientation on the in-cylinder air-water interaction, water evaporation, vapour distribution, performance and emission characteristics of a wall-guided GDI engine. It also presents the effects of water injector location and orientations on water evaporation rate, water droplet distribution, heat release rate, IMEP, and exhaust emissions. In this study, the spark-plug is considered as located in the middle of the cylinder head, and the water injector is mounted in between the exhaust valves. Four locations of the water injector (21 mm, 25 mm, 29 mm, and 33 mm from the spark-plug) are considered for the investigation. Also, the injector orientation is varied from 12° to 28°, in the step of 4°. The engine is operated under naturally aspirated and full-load conditions at an engine speed of 2000 rev/min. Analysis of results shows that the water evaporation rate increases when more amount of water is sprayed in the region where the velocities of water droplets are in the opposite direction of that of the in-cylinder air. It is found that the water injector located at 29 mm with the orientation of 24° is found to be optimum configuration, where the IMEP improved by about 9.2%, while NOx and soot emissions reduced by about 48.2% and 22.6% respectively compared to those of the case of no_water.
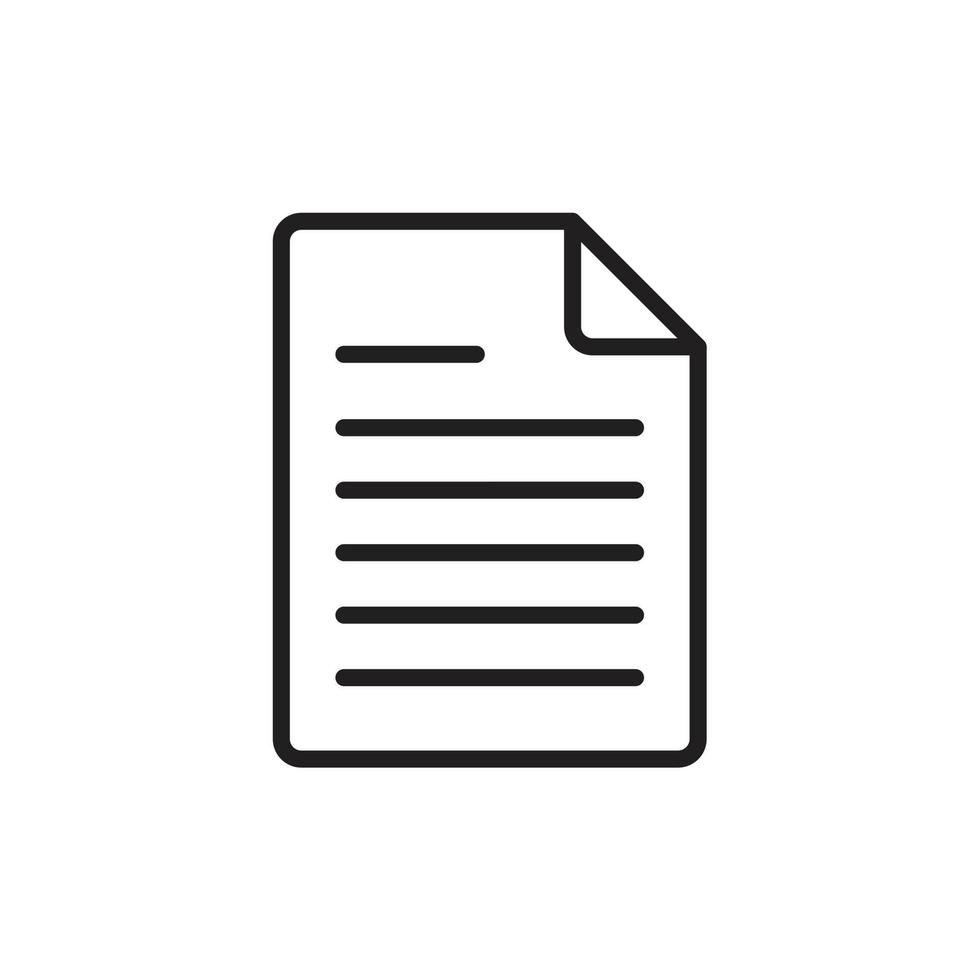
Effect of piston shape on in-cylinder flows and air-fuel interaction in a direct injection spark ignition engine - A CFD analysis
01-03-2015, Harshavardhan, Ballapu, Mallikarjuna J M
DISI (Direct injection spark ignition engines) are very popular today because of their low fuel consumption and exhaust emissions due to their operation at lean stratified mixture. Their performance depends on the level of mixture stratification, which in turn depends on in-cylinder flows and air-fuel interaction at the time of fuel injection. However, these are very much affected by combustion chamber configuration, which in turn is mainly dependent upon the piston shape. In this study, a CFD (computational fluid dynamics) analysis is carried out to analyze in-cylinder air flows and air-fuel interaction created by different piston shapes viz., flat, flat-with-center-bowl, inclined and inclined-with-center-bowl pistons in a four-stroke engine at an engine speed of 1500rev/min. Here, a start of fuel injection is considered at end of the suction stroke with a multi-hole injector operating at an injection pressure of 500bar. Engine specifications are selected from the literature for which experimental data is available for comparison. Finally, it is found that flat-with-center-bowl piston results in about 51% higher tumble ratio and about 21% higher turbulent kinetic energy of in-cylinder flows, better mixture stratification along with 33% higher evaporation rate and 33% higher percentage of fuel evaporation as compared to those of flat piston.
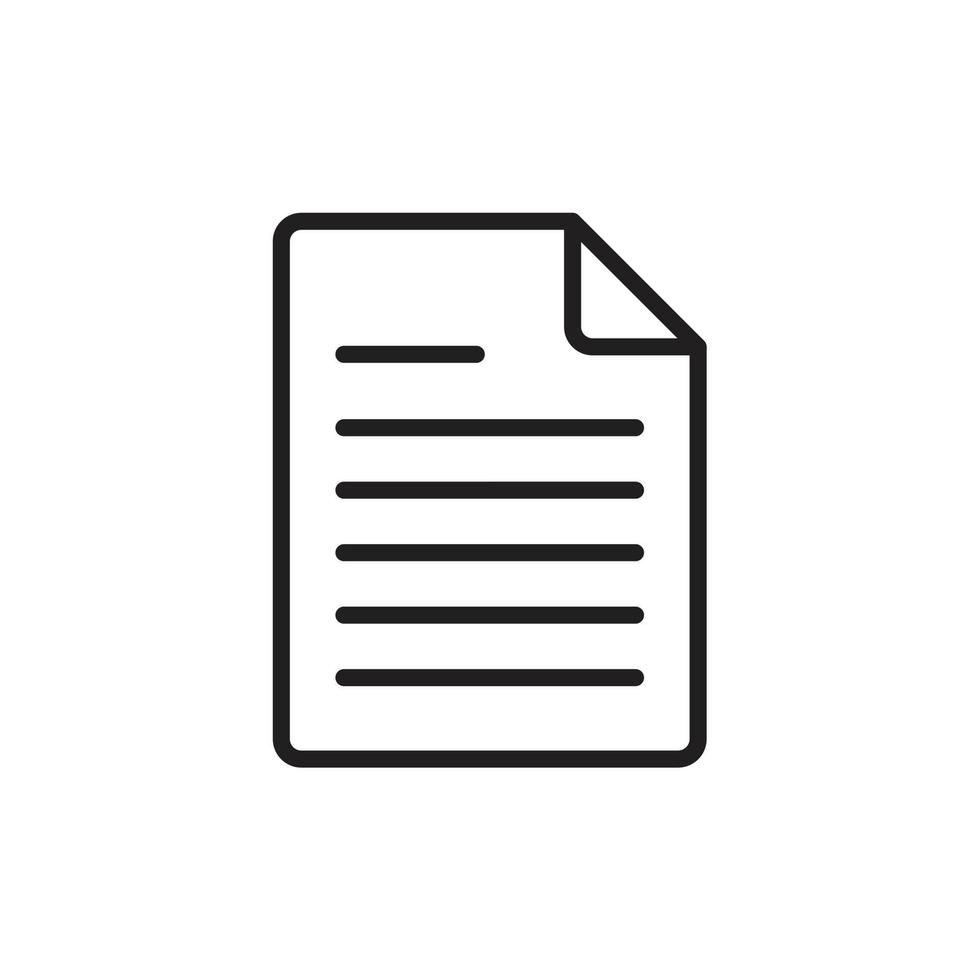
Optimization of Intake Port and Pentroof Angle for Simultaneous Reduction of Fuel Consumption and Exhaust Emissions in a Gasoline Direct Injection Engine
04-02-2020, Saw, Om Prakash, Addepalli, Srinivasa Krishna, Mallikarjuna, J. M.
This article aims to identify the best combination of intake port angle (IPA) and cylinder head pentroof angle (PA) of a gasoline direct injection (GDI) engine to achieve a simultaneous reduction in the fuel consumption and the exhaust emissions using computational fluid dynamics (CFD) and optimization techniques. The present study is carried out on a single-cylinder, four-stroke GDI engine. The design space is bound by the range of the IPA (35°, 80°) and the PA (5°, 20°). The initial data set consists of 80 design points, which are generated using the uniform Latin hypercube (ULH) algorithm. CFD simulations were carried out at all the points in the initial data set using CONVERGE at engine speed of 2,000 rev/min and the overall equivalence ratio of 0.7 ± 0.05. A prediction model based on the support vector machine algorithm is generated between the design inputs and the output parameters viz., indicated specific fuel consumption (ISFC), hydrocarbon (HC), nitric oxides (NOx), and soot. After sufficient validation of the prediction model, it is used for the optimization study. The optimization is carried out using the MOGA-II algorithm. The optimization study predicted that the IPA of 58° and the PA of 13.4° results best, in simultaneous reduction of the fuel consumption and the emissions. The results of the optimization study are further validated using the CFD analysis, which is carried out at the optimum design point. From the results, it is concluded that the optimization-driven design techniques could be effectively used to improve the engine performance and reduce the emissions simultaneously.
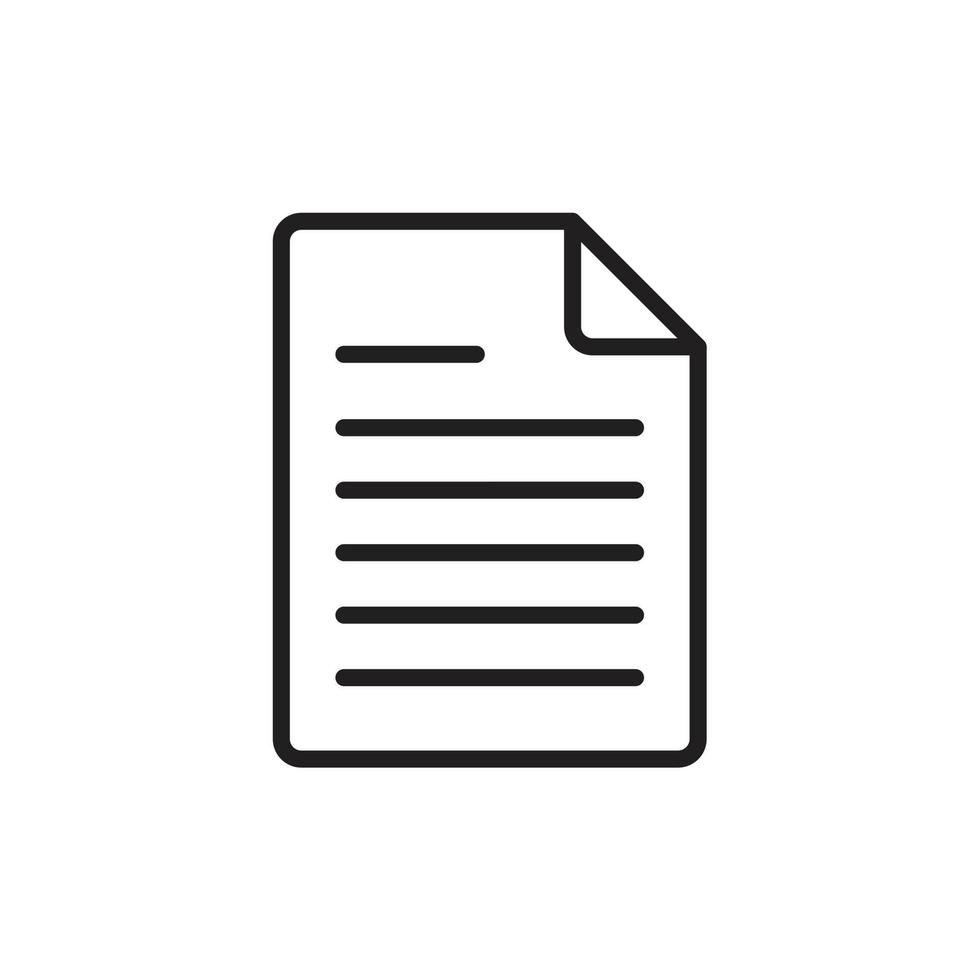
Effect of Fuel Injection Pressure on Mixture Stratification in a GDI Engine - A CFD Analysis
08-10-2017, Saw, Om Prakash, Karaya, Yashas, Mallikarjuna, J. M.
The mixture formation in gasoline direct injection (GDI) engines operating at stratified condition plays an important role in deciding the combustion, performance and emission characteristics of the engine. In a wall-guided GDI engine, piston profile is such that the injected fuel is directed towards the spark plug to form a combustible mixture at the time of ignition. In these engines, fuel injection pressure and timing play an important role in creating a combustible mixture near the spark plug. Therefore, in this study, an attempt has been made to understand the effect of fuel injection pressure with single and split injection strategy on the mixture formation in a four-stroke, wall-guided GDI engine operating under stratified conditions by using computational fluid dynamics (CFD) analysis. Four fuel injection pressures viz., 90, 120, 150 and 180 bar are considered for the analysis. All the CFD simulations are carried out at the engine speed of 2000 rev/min., compression ratio of 11.5, with the overall equivalence ratio of about 0.65. The fuel injection and spark timings are maintained at 605 and 705 CADs respectively. In this study, the effect of fuel injection pressure on mixture stratification is carried out by a new parameter called "Stratification Index". It is found that, at the time of the spark, with single fuel injection, with the fuel injection pressure of 180 bar, proper mixture stratification is produced. But, with split injection mode, at all the fuel injection pressures considered, a nearly homogeneous mixture is produced. Also in the single fuel injection cases, with the fuel injection pressures of 120, 150 and 180 bar, the peak in-cylinder pressures are higher by about 4.6, 14.9 and 19.6%; and 1.5, 3.7 and 4.3% respectively, compared to that of 90 bar fuel injection pressure.
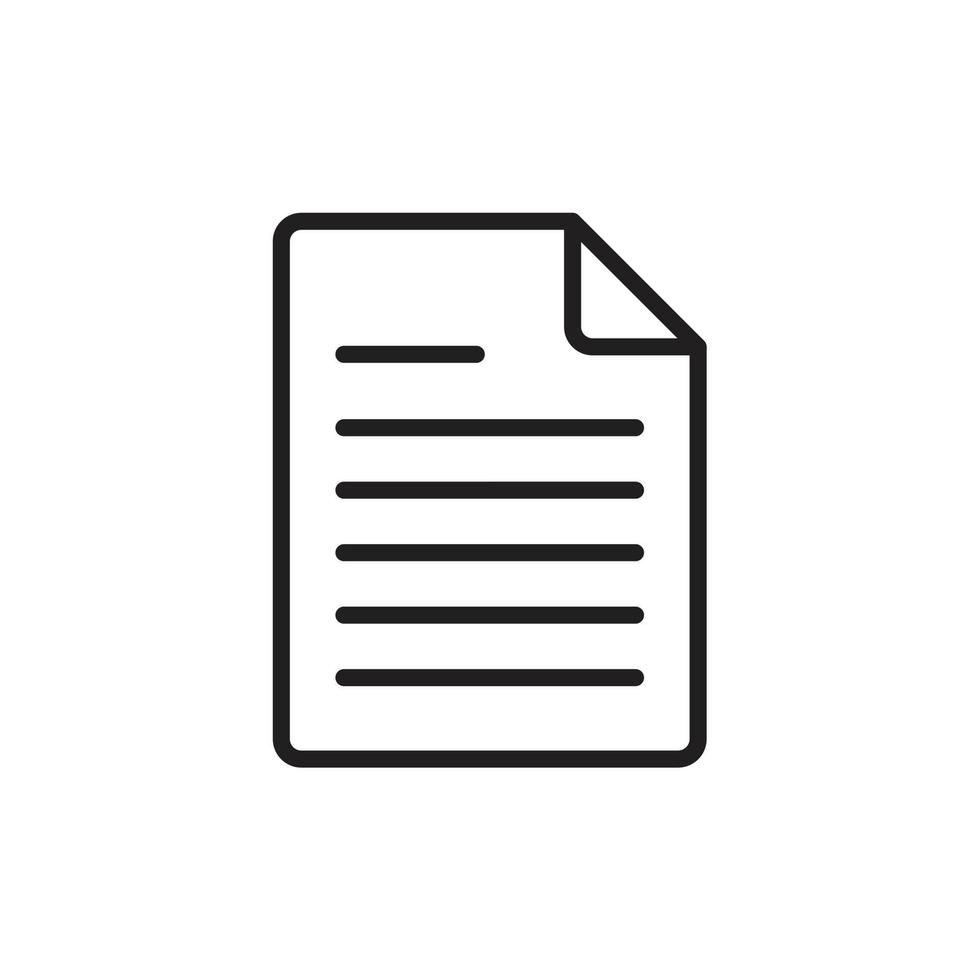
Effect of Water Injection and Spatial Distribution on Combustion, Emission and Performance of GDI Engine-A CFD Analysis
01-01-2018, Raut, Ankit Ashokrao, Mallikarjuna, J. M.
Water injection in diesel engines is a successful way to reduce NOx emissions and enhance brake power output. The advantages of water injection are because of its high enthalpy of vaporization and high specific heat capacity by which it absorbs heat from the in-cylinder mixture. The benefits of water injection depend on the rate of water vaporization and its spatial distribution in the combustion chamber. However, detailed effects of these parameters are very rarely studied in the past. Therefore, in the present study, an attempt has been made to assess the effect of water injector configuration on performance of a GDI engine by CFD analysis. Here, the analysis is done mainly to study and enhance the evaporation and spatial distribution characteristics of the water injection inside the combustion chamber. Water is directly injected into the cylinder of a naturally aspirated, four-stroke GDI engine. Various water injection configurations formed by different spray patterns and injector orientations are considered for the study and compared with a no water case. The analysis is done under full-load conditions with a constant engine speed of 2000 rev/min. The CFD models used in this study are validated from the available data in the literature. From the results, it is found that the water spray pattern in a shape of the regular hexagon at an injector orientation of 25 produces higher IMEP with lower NOx and soot emissions.
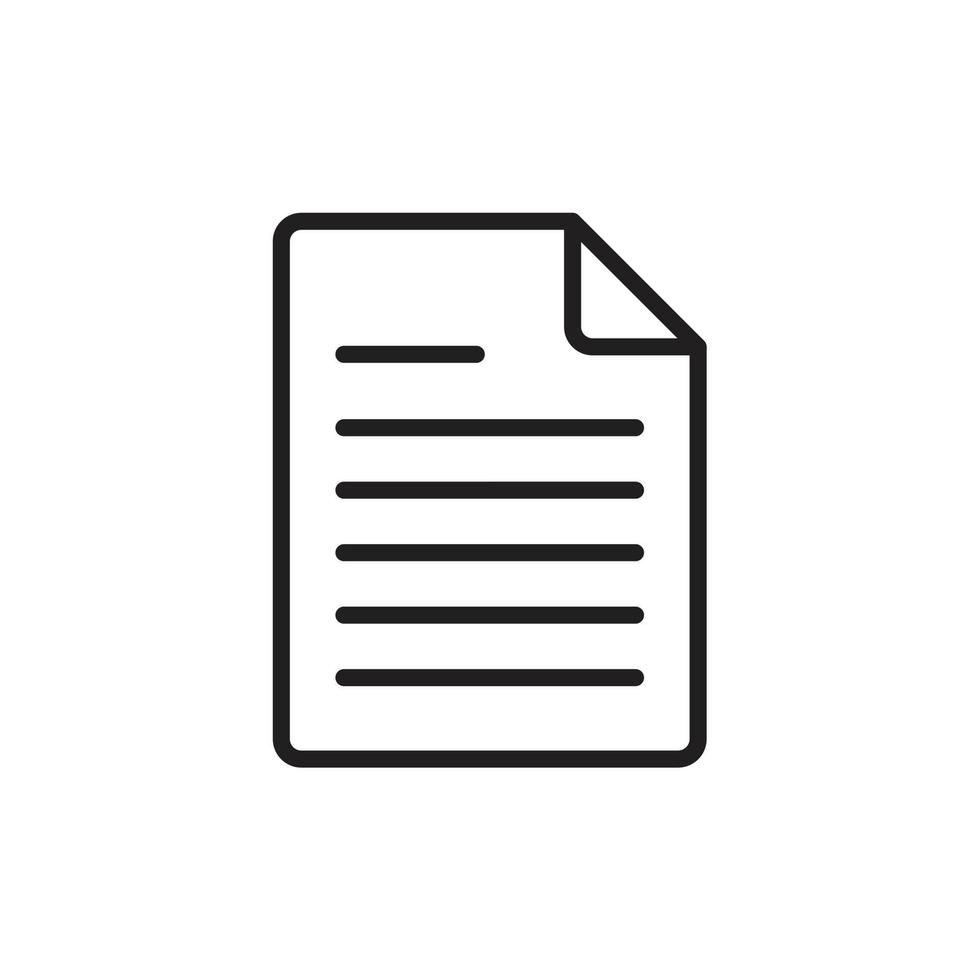
Effect of engine parameters on in-cylinder flows in a two-stroke gasoline direct injection engine
15-08-2016, Krishna, Addepalli S., Mallikarjuna J M, Kumar, Davinder
This paper deals with the in-cylinder flow field analysis in a two-stroke engine under motoring conditions by particle image velocimetry (PIV) and computational fluid dynamics (CFD). The main objective is to analyze the effect of engine parameters viz., engine speed, compression ratio (CR) and port orientation on the in-cylinder flows in a loop-scavenged two-stroke gasoline direct injection (GDI) engine, with an aim to help researchers to design fuel efficient and less polluting two-stroke engines. In this study, a single-cylinder 70 cm3 two-stroke engine which is very commonly used for the two-wheeler application, is considered. The engine cylinder is modified to provide optical access into the in-cylinder region. The PIV experiments are conducted at various engine speeds viz., 500, 1000 and 1500 rev/min, and the plane averaged velocity vector fields obtained, are analyzed to understand the in-cylinder flow behavior. The CFD study is also carried out using the commercial CFD code, STARCD, to study and compare the in-cylinder flow parameters at various engine operating conditions. The CFD results are compared with the experimental results to the extent possible. The CFD predictions are found to be in good agreement with the experimental results. Therefore, the CFD analysis has been extended further to understand the effect of various engine parameters on the in-cylinder flows. We found that the turbulent kinetic energy and tumble ratio increased by about 25% and 20% respectively, when the engine speed was increased from 1000 to 1500 rev/min. Also, we found that the turbulent kinetic energy and tumble ratio decreased by about 13% and 26% when the compression ratio was increased from 7 to 8. In addition, we found that the port orientation, rather than port areas had a greater influence on the in-cylinder flow parameters.
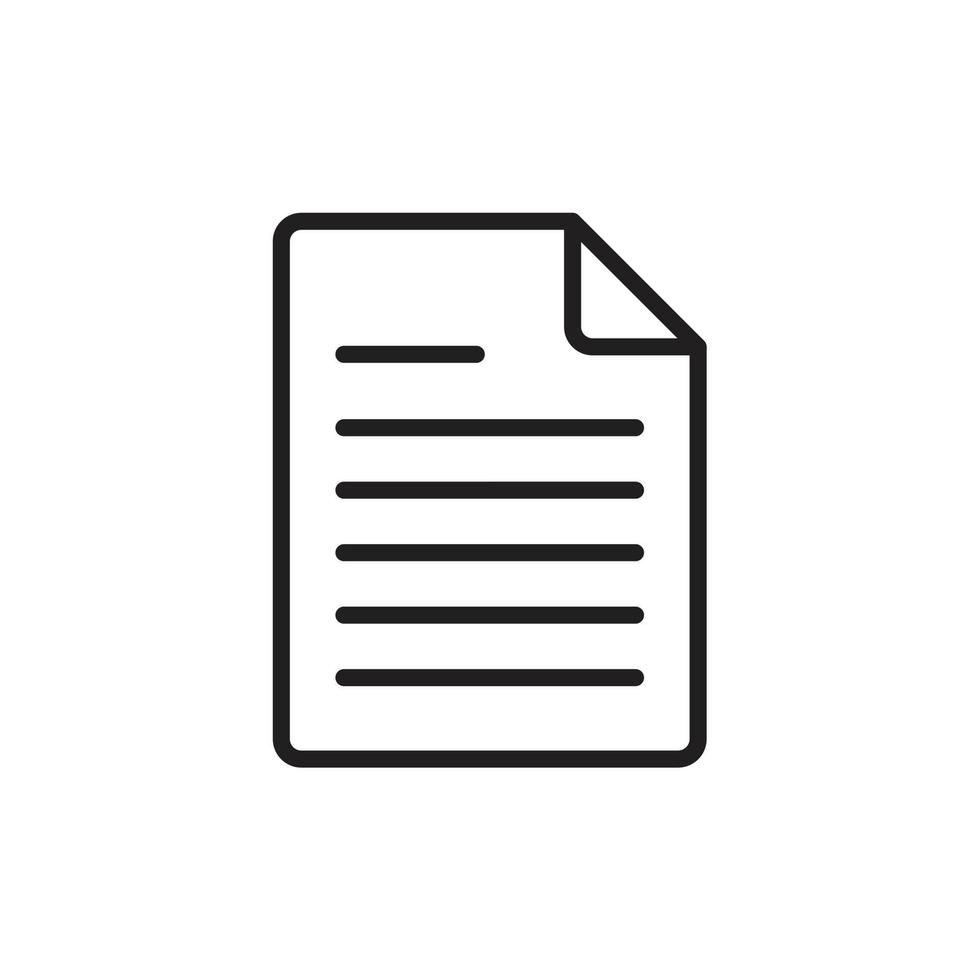
Effect of Mixture Distribution on Combustion and Emission Characteristics in a GDI Engine - A CFD Analysis
01-01-2017, Addepalli, S. Krishna, Saw, Om Prakash, Mallikarjuna J M
Mixture distribution in the combustion chamber of gasoline direct injection (GDI) engines significantly affects combustion, performance and emission characteristics. The mixture distribution in the engine cylinder, in turn, depends on many parameters viz., fuel injector hole diameter and orientation, fuel injection pressure, the start of fuel injection, in-cylinder fluid dynamics etc. In these engines, the mixture distribution is broadly classified as homogeneous and stratified. However, with currently available engine parameters, it is difficult to objectively classify the type of mixture distribution. In this study, an attempt is made to objectively classify the mixture distribution in GDI engines using a parameter called the "stratification index". The analysis is carried out on a four-stroke wall-guided GDI engine using computational fluid dynamics (CFD). All CFD sub-models used, in this study, are validated with the available experimental and CFD results from the literature before carrying out the analysis. Three types of mixture distributions viz., ideally homogeneous, ideally stratified and mal-distributed mixtures are defined and their effect on combustion, performance and emission characteristics of the engine are analyzed. Further, the effect of fuel injector orientation on the mixture distribution in the combustion chamber is analyzed for three different orientations of the fuel injector viz., -15, 0 and 15° with the vertical. From the results, it is found that the early fuel injection doesn't produce an ideally homogeneous mixture. Also, among the cases of the stratified mixtures, it is found that, the fuel injector orientation of 15° results in a mixture that is closer to the ideally stratified one. This is characterized by the value of stratification index that is close to 1.
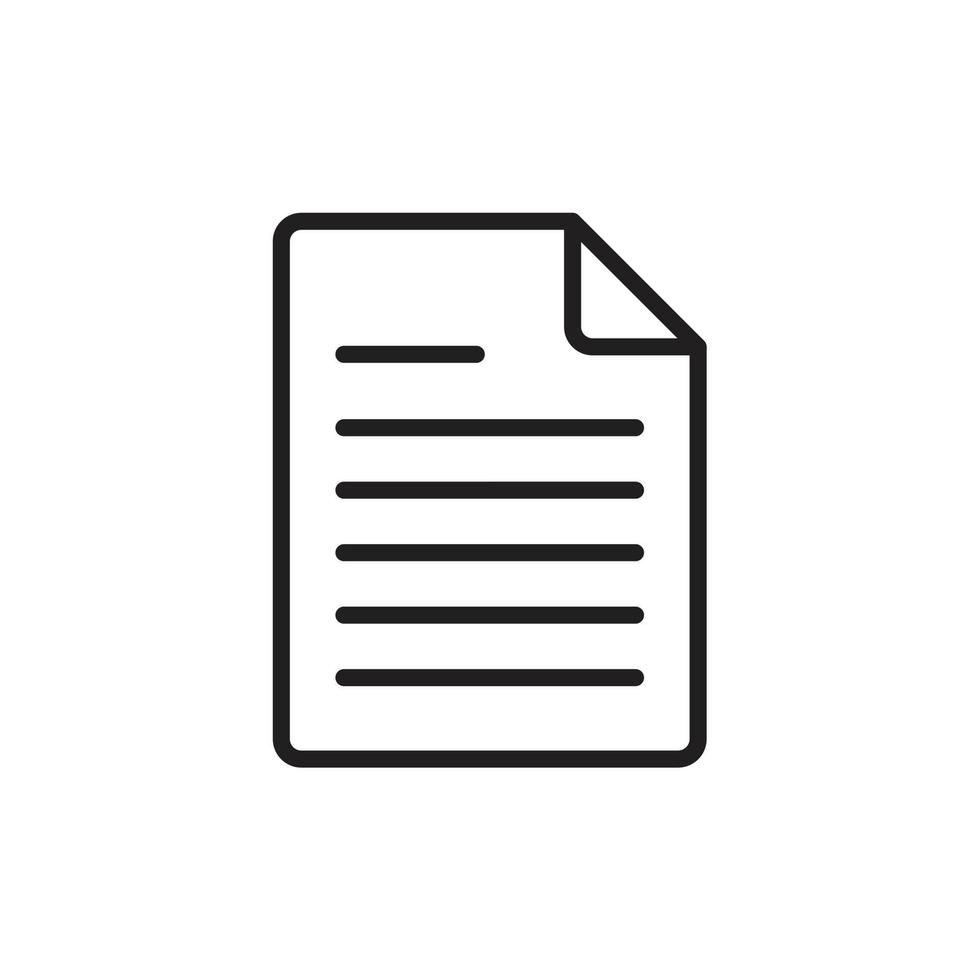
Flow investigation on different combustion chamber configuration in a DI diesel engine - A CFD approach
15-05-2012, Gnana Sagaya Raj, A., Mallikarjuna J M, Ganesan, V.
The main objective of the present investigation is to make a computational study of flow structure inside the engine cylinder in a DI diesel engine during the end of compression stroke at an engine speed of 1000 rev/min. The analysis has been carried out for four different piston configurations viz., flat piston, centre bowl on flat piston, inclined and inclined offset bowl piston. A polyhedral trimmed cell has been adopted for meshing the geometries using the code called STAR-CD Es-ice. The flow has been simulated by solving the governing equations of conservation of mass, momentum and energy using the SIMPLE algorithm. From this numerical prediction, the best possible combustion chamber configuration and the location of fuel injector on the cylinder head have been arrived. © (2012) Trans Tech Publications.